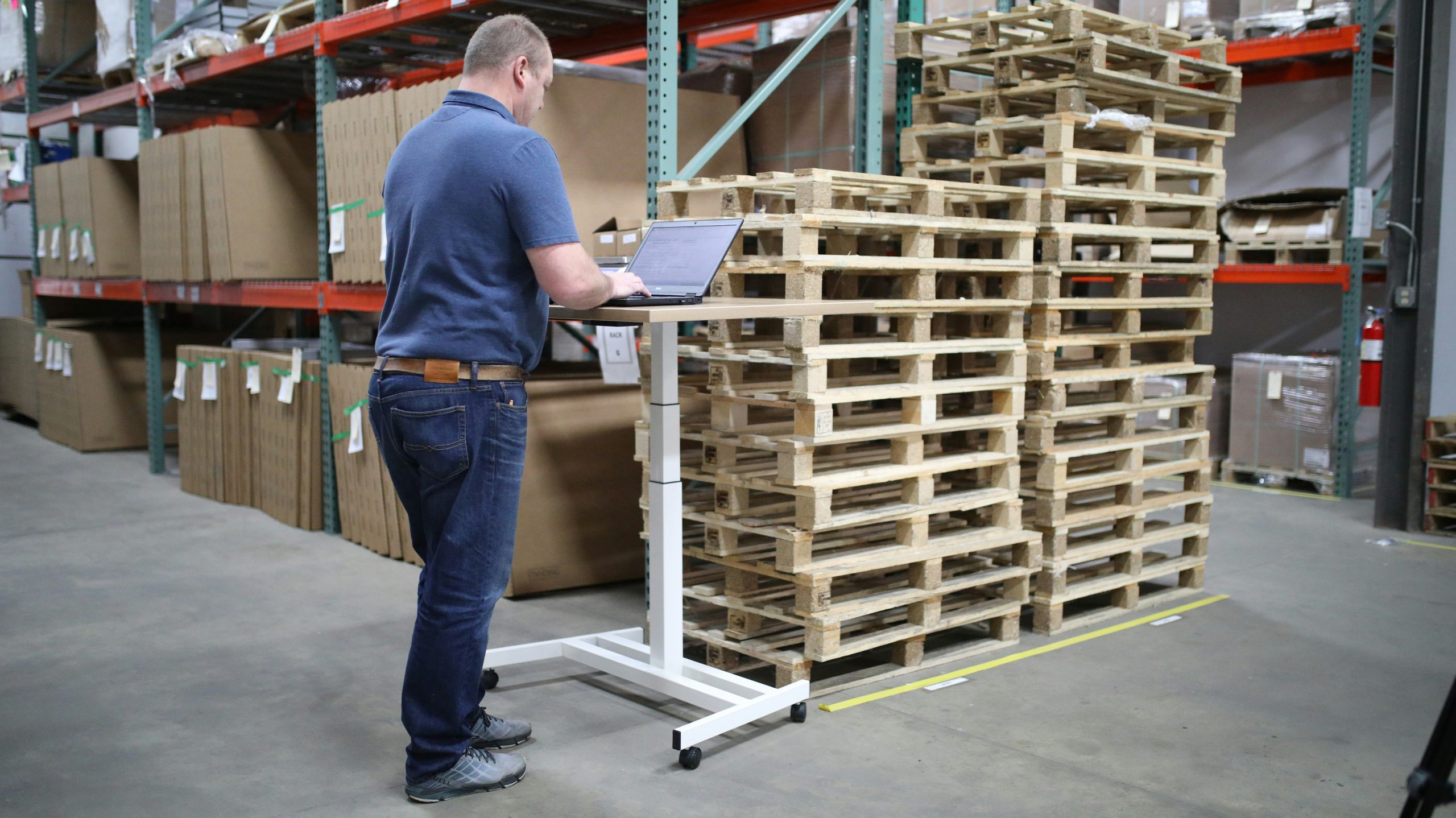
The logistics and warehousing sectors are undergoing a significant transformation with the introduction of Autonomous Mobile Robots (AMRs). These advanced machines promise to enhance efficiency, reduce labor costs, and streamline operations. However, successful implementation of AMRs in a warehouse setting requires careful planning and execution. Here’s a comprehensive guide on how to effectively integrate AMRs into your warehouse operations.
1. Understand Your Needs and Objectives
Assess Current Operations
Before implementing AMRs, it’s crucial to conduct a thorough assessment of your current warehouse operations. Identify bottlenecks, inefficiencies, and areas where automation can bring the most significant benefits. This could include tasks like inventory management, picking and packing, or internal transportation.
Define Clear Objectives
Establish clear, measurable goals for what you aim to achieve with AMRs. Objectives might include reducing order processing time, lowering labor costs, improving accuracy, or increasing throughput. Having well-defined goals will guide the implementation process and help measure the success of the integration.
2. Choose the Right AMRs for Your Needs
Types of AMRs
There are various types of amrs robots for warehouses, each suited for different tasks. Some common types include:
- Goods-to-person robots: Move inventory to workers for order fulfillment.
- Autonomous forklifts: Handle pallet transportation and stacking.
- Inventory robots: Perform stock counts and track inventory levels.
Select the type(s) of AMRs that align with your operational needs and objectives.
Evaluate Vendors
Not all AMR solutions are created equal. Evaluate different vendors based on their technology, support services, and track record. Consider factors like ease of integration with existing systems, scalability, customization options, and customer support.
3. Prepare Your Warehouse for AMRs
Infrastructure Upgrades
Implementing AMRs may require upgrades to your warehouse infrastructure. This could include enhancing Wi-Fi connectivity, ensuring smooth and obstacle-free pathways, and setting up charging stations for the robots. Additionally, you might need to install sensors or markers that help AMRs navigate the warehouse.
Integration with Existing Systems
Ensure that the AMRs can seamlessly integrate with your existing warehouse management system (WMS). This integration allows for real-time data exchange, which is essential for coordinating tasks between human workers and robots. Work with your WMS provider and the AMR vendor to facilitate this integration.
4. Train Your Workforce
Operational Training
Your workforce needs to be trained to work alongside AMRs effectively. This includes understanding how the robots operate, how to interact with them, and what to do in case of malfunctions. Providing hands-on training sessions and creating clear, accessible operational manuals can help ease this transition.
Safety Training
Safety is paramount when integrating robots into a human-centric environment. Conduct comprehensive safety training to ensure that employees understand the safety protocols related to AMRs. This includes maintaining a safe distance, understanding the robots’ navigation patterns, and knowing emergency procedures.
5. Pilot Testing and Gradual Implementation
Start with a Pilot Program
Begin with a pilot program to test the AMRs in a controlled environment. This allows you to evaluate their performance, identify any issues, and make necessary adjustments before a full-scale rollout. During this phase, closely monitor key performance indicators (KPIs) such as task completion time, error rates, and overall efficiency.
Iterate and Improve
Use the insights gained from the pilot program to refine your implementation strategy. Address any technical issues, optimize workflows, and adjust training programs as needed. Iterative improvements based on real-world data will ensure a smoother transition during full-scale implementation.
Gradual Rollout
Implement the AMRs gradually across different areas of your warehouse. This phased approach helps minimize disruptions and allows for continuous learning and adaptation. Start with high-impact areas and expand as confidence in the technology and processes grows.
6. Monitor Performance and Optimize
Continuous Monitoring
After full implementation, continuously monitor the performance of your AMRs. Use analytics and reporting tools to track metrics such as productivity, accuracy, downtime, and maintenance needs. Regular monitoring ensures that the robots are meeting your operational goals and allows for timely interventions when issues arise.
Maintenance and Updates
Regular maintenance is crucial to keep the AMRs operating efficiently. Develop a maintenance schedule in collaboration with the AMR vendor and ensure that your staff is trained to perform routine checks. Additionally, keep the robot’s software updated to benefit from the latest features and improvements.
Feedback Loop
Establish a feedback loop with your warehouse staff to gather their insights and experiences with the AMRs. Workers on the floor often provide valuable feedback on operational challenges and areas for improvement. Use this feedback to continuously refine and optimize the integration.
Conclusion
Implementing AMRs in your warehouse can revolutionize your operations, leading to increased efficiency, reduced costs, and improved accuracy. However, successful integration requires careful planning, selection of the right technology, workforce training, and continuous monitoring and optimization. By following these steps, you can ensure a smooth transition to a more automated, efficient, and productive warehouse environment. Embrace the future of warehousing with AMRs and stay ahead in the competitive logistics landscape.